Industrial Decarbonization: A Path towards Greener Manufacturing
In the journey towards Net Zero, pioneering green technologies in heavy industry are revolutionizing the production of steel, cement, hydrogen, and heat pumps.
Heavy industries develop everyday products that are central to our way of life, but due to their manufacturing processes, these industries are also responsible for nearly 40% of global carbon dioxide (CO₂) emissions. Their emissions amount to around 6 billion tonnes per year, more than one-sixth of total CO₂ emissions from the global energy system. Steel, cement, infrastructure and petrochemicals are the top emitting industries and are among the most challenging to decarbonize, owing to technical factors such as the need for very high temperatures and process emissions of carbon dioxide, and economic factors including low profit margins, capital intensity, long asset life, and trade exposure.
Industrial decarbonization refers to the process of reducing or eliminating carbon emissions from industrial activities. This is a sector which revolves around machines, molecules and atoms. While software is an enabler, it is not the main driver for the emissions reduction - rather, it is the hard assets, product and infrastructure that will derive the most value out of a push towards decarbonization. Governments and regulatory bodies play a crucial role in driving industrial decarbonization. Policy measures such as carbon pricing and tax, emissions standards, and financial incentives can encourage industries to adopt cleaner technologies and practices. With strong regulatory tailwinds, this sector will be a major driver in the path towards net zero.
Continued R&D in new technologies and processes can lead to breakthroughs in materials, production methods, and energy storage, making it easier for industries to reduce their carbon footprint.
In particular, deep decarbonization of the steel and cement industries will require several parallel strategies: demand management through market creation and circular economy principles, improvements in energy efficiency through technological advancements, and major shifts in production methods and technology. In this article, we deep dive into three major sub-sectors within industrial decarbonization: i) Green Steel; ii) Green Cement and iii) Heat Pumps.
I. Green Steel
If steel were a country, it would be the third largest carbon dioxide emitter and the second largest coal consumer. Approximately 2 billion tons of steel is produced annually, which contributes to 7-9% of global carbon emissions. Close to 75% of steel is produced via the highest emitting blast furnace methods in which the production of coke and the reduction of iron ore are the stages where carbon dioxide is emitted.
As shown in Figure 1, most of the world’s steel is produced via i) blast furnaces which produce iron from iron ore, and ii) basic oxygen furnaces which turn that iron into steel. The process is inherently carbon and temperature intensive, using metallurgical coke produced by destructive distillation of coal in a coke oven, which reacts with the oxygen in the hot air blast to produce carbon monoxide. This reacts with the iron ore in the furnace to produce CO₂.
There are multiple ways to reduce such emissions:
Scrap based EAF: A 95% reduction in carbon intensity is possible by way of transitioning to scrap metal, recycled steel bar, powered by electric arc furnaces (EAF). Hybar is a US-based company building in this space, whose technology is designed to significantly reduce the amount of energy needed to produce reinforced steel.
Alternate Energy: Using alternatives for coal or utilizing waste heat to improve overall efficiency can also reduce carbon emissions. H2 Green Steel is a Swedish company which abates emissions by 95% compared to traditional blast furnace production processes, by replacing coal with green hydrogen, using electricity from renewable sources as well as digitization and AI at the process level.
Closed Loop Carbon Recycling System: This involves capturing CO₂ from the blast furnace gas and reduces it to CO using a crystalline mineral lattice known as a ‘perovskite’ material. This material lowers the range of temperatures (700-800 degrees Celsius) to produce steel, that can be either powered by renewable energy sources and/or generated using heat exchangers connected to the blast furnaces. The University of Birmingham Enterprise has arrived at this novel method which is currently in research phase at present, but holds high potential in being retrofitted to existing steel plants rather than building new EAF facilities.
If these methods are successful, the end-product of green steel will be very low carbon, high-quality flat steel, targeting mainly the automotive, construction, white goods, industrial equipment and energy sectors.
The two challenges with green steel include: i) high upfront capital expenditure costs; and ii) uncertainty around which of the above technologies will prevail, since they are still in the pilot stage.
Established players in India are innovating in this space. For example, Tata Steel has carried out trials with hydrogen injection in blast furnaces and it has installed carbon capture plants in some its manufacturing facilities. Furthermore, JSW Steel, India’s second-largest maker of the alloy, plans to establish a green steel manufacturing facility by 2030, and separately plans to establish an electric arc furnace plant based on direct reduced iron (DRI) technology.
The shift towards net zero steel would likely depend on a collaborative effort among regulators, governments, financiers and industry stakeholders to change the economics of production, facilitate access to required capital, and stimulate demand for green steel. From the private sector’s innovation perspective, the focus should be on solutions that do not require special regulatory adjustments but rather can be embedded in existing processes and are price competitive compared to current processes.
II. Green Cement
Cement, on the other hand, is a US$ 900 Bn market and it is the second most consumed product globally, after water. Cement is mainly used as a binder in concrete, and the latter is a basic material for all types of construction, including housing, roads, dams and ports, as well as for decorative applications (patios, floors, staircases, and furniture). Cement production contributes approximately 8% of greenhouse gas emissions, primarily originating from two sources: i) generating the heat used to convert its raw materials, namely limestone, into clinker, the direct precursor to cement itself; and ii) the chemical reaction that occurs when limestone is sintered, splitting the rock into lime and carbon dioxide gas.
Green cement is an eco-friendly cement that uses a carbon-negative process of manufacturing. Low-carbon cement helps reduce the “embodied carbon” footprint of buildings. There are multiple ways to reduce emissions while manufacturing cement, for example:
Formulation changes by using clinker substitutes: Slag from the blast furnace and fly ash are the chief materials used in the manufacturing of green cement and boosting the effectiveness of equipment. Changing the formulation (in other words, lowering the proportion of limestone), and blending in low-carbon substitutes, can result in lower emissions. Alternatively, adding CO₂ to concrete cures can strengthen the solid material and reduce the quantities needed. BioMason, a US based company, produces bio cement where the production combines natural microorganisms and chemical processes to develop masonry materials at room temperature, which helps replace traditional clay and concrete, and the high energy consumption associated with standard manufacturing them, enabling builders to purchase low-carbon building materials.
Carbon Capture: Carbon capture involves chemically or physically capturing the carbon emissions released from industrial waste during the fuel-burning process. In the green cement sector, Cocoon Carbon is an example of a company whose technology captures carbon into industrial waste before processing it into sustainable building materials, enabling businesses to efficiently mineralize waste on or near the site, with minimal disruption and no capex. Materials such as steel slag, cement kiln dust, biomass ash, fly ash, mine tailings, and demolition waste have enormous carbon capture and up-cycling potential. Not only does the supplementary material have a low carbon footprint, but it also permanently stores CO₂.
Alternative energy sources: Other opportunities include replacing fossil fuels with renewable electricity. Sublime Systems is building an electrochemical platform that converts limestone to lime at room temperature, making the CO₂ produced during the conversion process easier to capture, and reducing overall energy consumption.
At a global level, established players in the conventional cement industry are also innovating towards making their processes greener. Heidelberg Materials in Norway is building an industrial-scale carbon capture plant in its cement factory, that could capture and store an estimated 400,000 tons of CO₂ annually. Moreover, in India, Dalmia Cement has developed a partnership with SaltX aiming to complete a joint pilot plant for electrically produced cement by 2024 that will incorporate SaltX's Electric Arc Calciner (EAC) technology at one of Dalmia's existing plants in India. Furthermore, JSW’s Green Crete Smart Range reduces emissions from 25-40 %, as it uses low-CO₂ supplements (supplementary cementitious materials – Ground Granulated Blast-furnace Slag) as a partial replacements for ordinary Portland Cement.
III. Heat Pumps
Approximately 50% of all energy consumed in the EU is used for heating and cooling, and more than 70% still comes from fossil fuels (mostly natural gas). Heat pumps are a direct potential replacement for all heat generating activities in industries for which fossil fuels are being used presently. Instead of burning natural gas, a heat pump warms a building by transferring heat from the outdoor air or an existing low-temperature heat source, into an interior space.
This technology is 3x - 5x more energy efficient and more cost efficient than the average, fossil-fueled, Heating, Ventilation, and Air Conditioning (HVAC) system.
Today, industrial heat pumps are mainly used for low temperature processes below 100°C, notably in the paper, food and chemicals industries. However, output temperatures of up to 150°C can already be achieved if waste heat of about 100°C is available as an input. For temperatures between 150°C and 200°C, heat pumps need special refrigerants and compressors, for which technologies are still in an early prototype stage (Technology Readiness Level [TRL] 4-5).

Some of the interesting trends in heat pump technology include:
Decarbonizing industrial process steam through a modular, drop-in, electrified steam, heat-pump boiler. The use of steam with mechanical vapor recompression (MVR) equipment is used in a similar way to heat pumps (that is, using electricity to upgrade heat to a higher temperature). Atmos Zero is an example of a company innovating in this space, which intends to use as little as half of the electricity of today's electric boiler services.
Other companies use ‘hybrid electrification’, where heat pumps work in conjunction with radiators. The pumps run on electricity, which is increasingly sourced from clean wind and solar energy, while the radiator system runs on fossil fuels. Kelvin is an example of this type of technology which has developed a bespoke heat pump that replaces room air conditioners, works with a thermal battery, and shifts heating and cooling to 80% electricity in these legacy buildings.
There is large policy push for the adoption of heat pumps globally. In the USA, 30% tax credits are being offered with a cap of $2,000 to push installation of heat pumps under the Inflation Reduction Act (IRA). The UK is also setting a target of installing 600,000 heat pumps per year by 2028, and efforts are focused on cost reduction by at least 25-50% by 2025 and towards cost parity with boilers by 2030. Moreover, the EU has an annual sales of 3 million units now and a potential total stock of 80 million heat pumps. REPowerEU and The Green Deal Industrial Plan are the flagship policies calling for frontloading investments in renewables and energy efficiency. Interestingly, given the large outlay of cash from heat pumps, 66% of the entire value chain will require financing to procure the heat pumps by 2030, and we believe that there is large untapped opportunity in the sector.
Looking Ahead
In summary, industrial decarbonization technologies have made strong headway in disrupting the carbon footprint of heavy industry. However, there is a need for more cost-effective manufacturing technology to enable widespread adoption at scale.
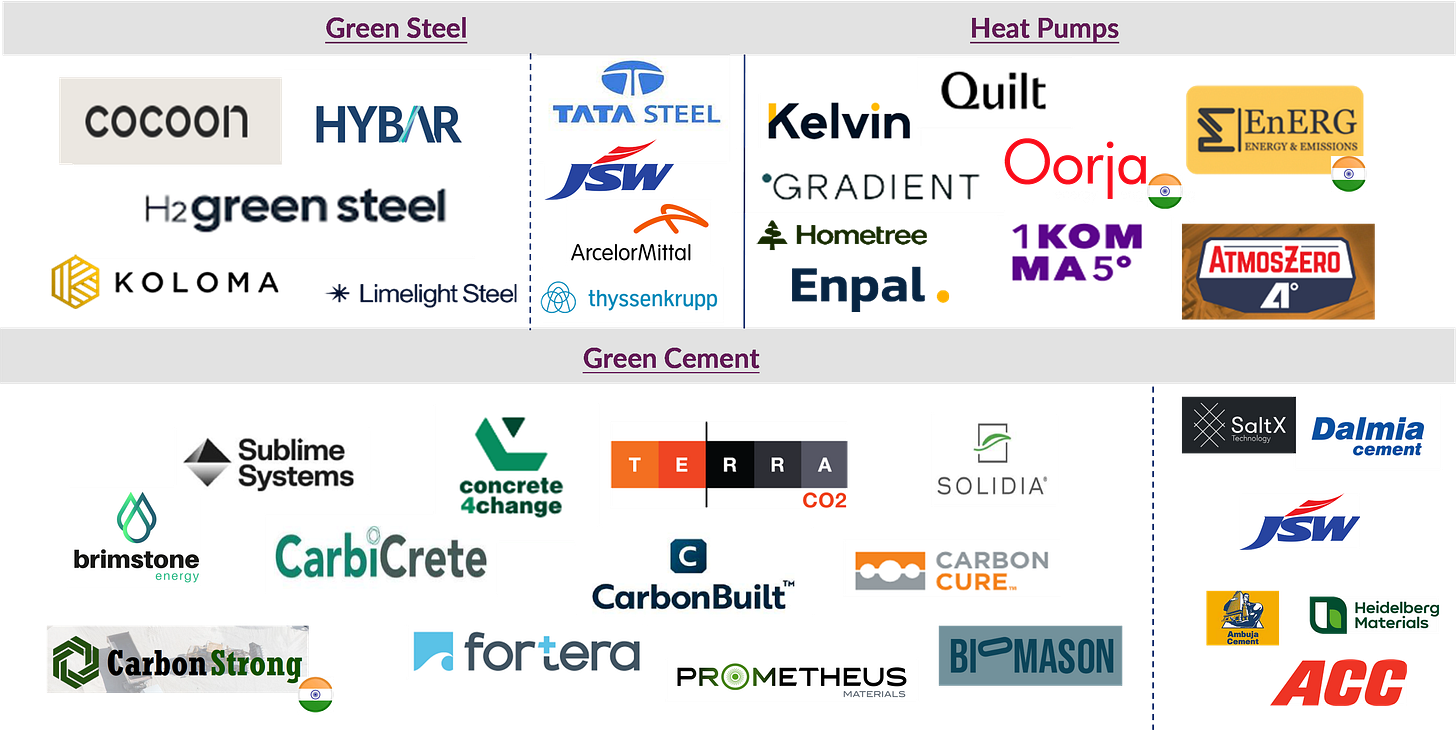
As Figure 4 shows, while the larger companies are creating breakthroughs in this space, on the early stage spectrum, green steel, green cement and heat pumps technologies are at nascent stages. However, we see plenty of opportunity for disruption if cost-effective solutions are explored at scale. Interestingly, a new wave of innovators are also exploring circular models in this space, such as the refining of industrial waste and sand, to decarbonize concrete. For example, Carbon Upcycling is a compelling example of this trend, where it takes industrial byproducts and natural materials from coal plants, glass manufacturing, mine sites to create superior additives into concrete, sequester Co2 and improve overall performance.
With combined efforts of investors and industry leaders to address common barriers related to policy, technology, and financing, the goal of industrial decarbonization is becoming increasingly attainable. At Theia Ventures, we are eager to collaborate with founders who are developing exciting innovations at the forefront of this ecosystem.